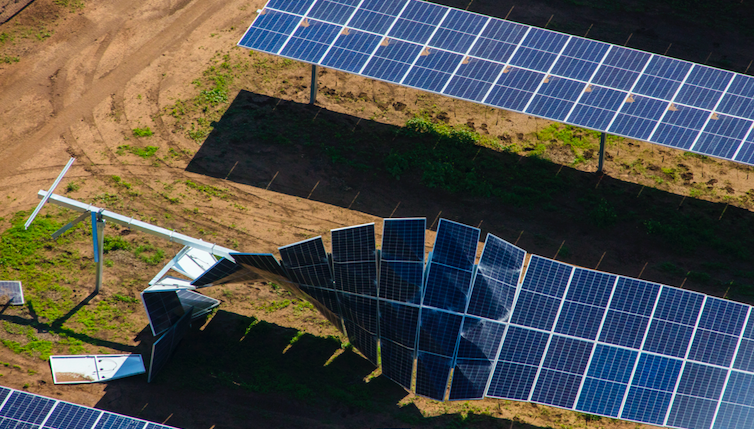
扭曲的组件说明了2018年10月在Oakey 2站点遭受的损坏。
NEXTracker的首席执行官Dan Shugar是美国太阳能兴起的老派参与者之一,对太阳能跟踪器了如指掌。
NEXTracker是全球领先的追踪器供应商,2018年出货量占市场的三分之一。其他公司分别占据8%至12%的市场,包括Array Technologies,PV Hardware,Arctech Solar和Soltec。
根据伍德·麦肯齐(Wood Mackenzie)的说法,跟踪器市场在2019年增长了62%,预计从2019年到2024年将达到23GW的安装量,该市场每年将平均增长11%。
在我们对 Shugar 的采访的第一部分中,我们讨论了跟踪器创新,双面组件以及如何被Flex收购。在我们讨论的最后一部分中,我们讨论了太阳能阵列中的大风环境下恐怖的扭转。
***
pv杂志的澳大利亚工作人员深入研究了单轴跟踪器在风力事件中的行为和失效方式,并指出单轴太阳跟踪器在相对适中的风速下变得不稳定。第三方工程公司已经研究了几种不同的跟踪器设计,这些设计在现场由于扭振而遭受了灾难性的故障。
1940年塔科马海峡大桥(Tacoma Narrows Bridge)的倒塌是一个典型的(非PV)扭转奔腾的例子。
这是扭矩管单轴跟踪器在风中疾驰的示例。
一些跟踪器设计旨在通过扭转刚度解决这种不稳定性,但这限制了跟踪器的长度,并且需要较厚的梁管径。其他供应商已经使用了阻尼,但是在某些跟踪器位置,阻尼的好处有限。
***
采访已被编辑和压缩。
光伏杂志:您想谈一谈扭动力吗?
丹·舒格:我想告诉你整个故事。首先,让我谈谈那个澳大利亚项目发生的事情。[ 昆士兰州的Oakey 2站点。]澳大利亚有两个项目-同时建设的项目。其中一个电站使用NEXTracker跟踪,另一个电站用的另一种厂家的跟踪,那家供应商将不愿透露姓名。
那里有两个系统,它们非常大,每个都有一百兆瓦。经过有两天的暴风雨,在每小时40英里~45英里的情况下。当所有尘埃落在上面时,NEXTracker系统的损坏为零。
另一个厂家却是严重的组件残骸[见文章照片]。他们的系统中没有失败的部分由于系统的布局方式而被我们屏蔽了。
其他供应商不受NEXTracker保护的部分损坏已深入到他们的系统中。
我们拥有悠久的历史,具有真正的风特征。如果您甚至回到PowerLight的日子,我们都在进行所有这些风洞研究。在理解结构上的风力时,相当直截了当的就是所谓的静态评估。当事情开始发展时,真正难做的是动态评估。
您不能在书中查找它。我们早在2015年在NEXTracker上就率先提出了这一要求-我们赞助了全球著名的风能工程公司开发此类结构(CPP),以动态方式表征跟踪器。
我们能够在实验室环境中复制并实际创建这些动态不稳定性,对其进行特征化,然后重新设计我们的产品以确保已解决。我们出版了此书,并允许CPP在2015年和2016年向我们公开发行作品。在2018年,我们决定发布很多对我们来说是核心IP的作品,因为其他一些人要么都不了解它或偷工减料-并对追踪器行业造成不负责任的破坏。
[NEXTracker博客文章指出David Banks及其团队在CPP进行的开拓性风洞研发工作,该工作研究了单轴跟踪器中的扭转不稳定性,涡旋锁定和其他因素。CPP的工作还研究了不同的存放方法,跟踪器设计架构以及适当的风能工程实践对LCOE的潜在影响。]
丹·舒格(Dan Shugar):世界各地发生了许多灾难性的失败。他们发生在澳大利亚,约旦,拉丁美洲和欧洲。
pv magazine:不仅仅是风的大小,还有其他所有动态变量吗?
丹·舒格(Dan Shugar):实际上,真正的高风速并不在乎。令人关注的是中等风速。原因是这些结构的固有振动频率约为1赫兹。根据结构的实际细节,它可以多一些或少一些。从共振的角度来看,这些结构可以在时速介于35英里和50英里之间的风中被激发。
您需要解决它。我们在NEXTracker上解决该问题的方法是,在系统上放置一堆阻尼器,然后实际测量风,然后实际收起风。如果您在街上行走,并且风在脸上飞,您将拥有一把雨伞,不要水平放置,而是想被风吹走。
这就是我们对地平线系统所做的事情。我们有2P两肖像产品。最大和最引人注目的故障是宽度为两个组件的2P。
光伏杂志:为什么?
丹·舒格(Dan Shugar):风力是悬臂的平方函数。当您将宽度扩大两倍时,您将获得400%的扭转力。发生的事情是,有许多竞争者将我们正在做的事情变成一幅肖像,然后将其放大一倍,缩放比例,然后说:“嘿,我们的基础更少了”,并获得了很多订单。
我们并没有贬低竞争对手,而是说:“嘿,你不能那样做。” 您不能仅仅依靠中心齿轮,而是依靠管子的刚度将疯狂的大帆固定在那里。
在设计初始产品时,我们希望打入市场的中间部分,这是典型的合理土壤,典型的合理风,典型的合理地面覆盖率。
与其他提供程序不同,我们解决该问题的方法是在结构中一直使用多个齿轮来锁定它,以防止它进入这种扭转不稳定性。从我们的角度来看,您不能仅仅依靠中心安装齿轮中管子的刚度。即使没有阻尼器,其中一些人现在仍在这样做,我们认为这完全是疯狂的。
看起来有很多方法可以解决工程问题-我们只是说,如果您要特别拍摄两幅肖像,您必须格外小心如何处理风力和动力。
原文
Dan Shugar, NEXTracker CEO, on solar trackers in wind and the terror of torsional galloping
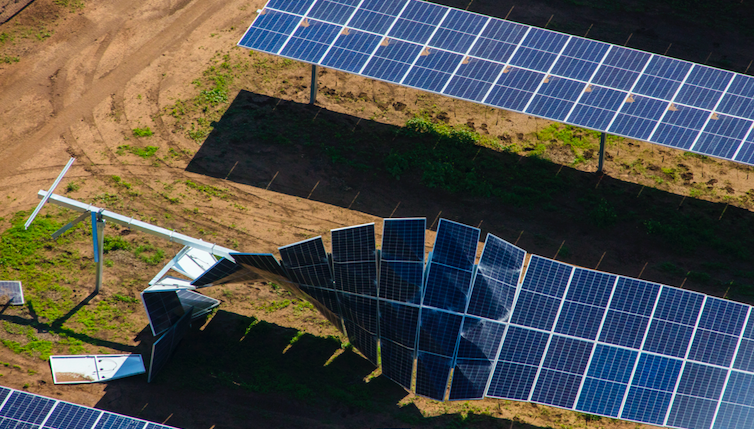
Twisted modules illustrate the damage incurred at the Oakey 2 site in October 2018.
Photo: Provided on an anonymous basis
Dan Shugar, CEO of NEXTracker, is one of the old-school players in the rise of solar in the United States — he lives and breathes solar trackers.
NEXTracker is the world’s leading tracker vendor, with one-third of the market by shipments in 2018. Other firms claim between 8 percent and 12 percent of the market each, including Array Technologies, PV Hardware, Arctech Solar and Soltec.
According to Wood Mackenzie, the tracker market grew 62 percent in 2019, reaching 23 gigawatts of installations — and the market will grow on average by 11 percent annually from 2019 through 2024.
In the first part of our interview with Shugar, we discussed tracker innovation, bifacial panels and getting acquired by Flex. In this final part of our discussion, we cover the terror of torsional galloping in a solar array.
***
pv magazine’s Australian staff has taken deep dives into how single-axis trackers behave and fail in wind events, noting that single-axis PV trackers become unstable at relatively modest wind speeds. Third-party engineering firms have studied several different tracker designs that have suffered catastrophic failures in the field as a result of torsional galloping.
A classic (non-PV) example of torsional galloping is the 1940 collapse of the Tacoma Narrows Bridge.
Here’s an example of a torque tube single-axis tracker galloping in the wind.
Some tracker designs have aimed to address this instability with torsional stiffness — but this limits the tracker length, and requires a thick torque tube. Others vendors have used damping, but damping can be of limited benefit in some tracker positions.
***
The interview has been edited and condensed.
pv magazine: Do you want to talk about torsional galloping?
Dan Shugar: I want to tell you the whole story. First, let me address what happened on that Australian project. [The Oakey 2 site in Queensland.] There are two projects in Australia — projects that were built concurrently. There’s a system with a NEXTracker, and there’s a system with another tracker. That vendor will go unnamed.
There are two systems there, they’re pretty big — a hundred megawatts each. There was a windstorm for two days in the mid-40 miles-an-hour, 45 miles-an-hour plus or minus. When the dust settled on all that, there was zero damage on the NEXTracker system.
The other system was a severe train wreck [see article photo]. The part of their system that didn’t fail was shielded by us because of the way the systems were laid out.
The section where the other vendor was not protected by NEXTracker had damage that went way deep into their system.
We have a long history with really characterizing wind. If you go back to even the PowerLight days, we were doing all these wind tunnel studies. What’s fairly straight forward in understanding wind force on structures is what’s called static evaluation. What’s really hard to do is dynamic evaluation — when things start moving.
You can’t look it up in a book. We pioneered this back in 2015 at NEXTracker — we sponsored the preeminent wind engineering company in the world for structures like this (CPP) to characterize trackers in a dynamic fashion.
We were able to, in a lab environment, replicate and actually create these dynamic instabilities, characterize it, and then re-engineer our product to make sure it was addressed. We published this and we allowed CPP to publish with credit to us in 2015 and 2016. In 2018, we made the decision to publish a lot of stuff which was core IP to us, because some of the other folks either didn’t understand it or were cutting corners — and were irresponsibly damaging the tracker industry.
[A NEXTracker blog entry notes the pioneering wind tunnel R&D work done by David Banks and his team at CPP, which investigated torsional instability, vortex lock-in and other factors in single-axis trackers. The CPP work also looked at the potential impact of different stowing approaches, tracker design architectures, and the LCOE implications of proper wind engineering practices.]
Dan Shugar: There were a bunch of catastrophic failures around the world. They’ve happened in Australia, Jordan, Latin America and Europe.
pv magazine: It’s not just the magnitude of the wind, but all these other dynamic variables?
Dan Shugar: Actually, the real high wind speeds are less of concern. It’s the medium wind speeds that are of concern. The reason is that these structures have a natural frequency of oscillation, which is about one Hertz. It can be a little more, a little less depending on the actual details of the structure. Those structures can get excited from a resonance standpoint in winds that are between, let’s say, 35 and 50 miles per hour.
You need to address it. The way we address it at NEXTracker is we put a bunch of dampers on the system, and we actually measure for the wind, and we actually stow into the wind. If you’re walking down the street and the wind’s blowing in your face, you have an umbrella, don’t be horizontal, you want to be into the wind.
That’s what we do with the horizon system. We have a 2P two-portrait product. The largest and most spectacular failures had been 2P, two modules in width.
pv magazine: Why is that?
Dan Shugar: The wind force is a squared function of the cantilever. When you go twice as wide you have 400% more torsional force. What happened was, there were a number of competitors that took what we were doing on one portrait, and then doubled it, scaled it and said, “Hey, we have less foundations,” and got a bunch of orders.
We’re not disparaging a competitor, but we’re saying, “Hey, you can’t do that.” You can’t just take a center gear and rely on the stiffness of the tube to hold this crazy big sail out there.
When we designed our initial product, we wanted to hit the middle part of the market, which is typical reasonable soil, typical reasonable wind, a typical reasonable ground cover ratio.
The way we address it, unlike the other providers, is we have multiple gears all the way down the structure to lock it, to prevent it from going into this torsional instability. From our viewpoint you can’t just rely on the stiffness of a tube in a center mount gear. Some of those guys are doing it now even without dampers, which we think is completely nuts.
Look there’s a lot of ways to solve the engineering problem — we’re just saying, if you go two-portrait in particular, you have to be extraordinarily careful about how you deal with wind force and dynamics.